This week we find ourselves at a key transition point in our brief history. Welcome to the second half of the 20th century.
Although Taiichi Ohno and W. Edwards Deming, did, in their own rights, many profound things in and outside of the commercial industry, by the middle of the 20th century there was a seed change occurring in the way that all of us would come to think about production, and about automation.
As the night dawns on one of our past heroes, a new one rises.
Henry Ford, born July 30, 1863, and died April 07, 1947, was for all intents and purposes of this history, the thought leader of thought leaders when it came to lean production of atoms.
Enter Eliyahu Goldratt, born 8 days before Ford died in 1947, on the other side of the world, in Mandatory Palestine. He would become a highly trained Ph.D. physicist before turning to business and is now best known for changing the way that MBA students think about bottlenecks, constraints, and optimization of the throughput of any production operation.
Don’t let his face on the cover of nearly every book he wrote hold you back; he was the real deal. He was actually that good, so I’m fine with it. As I’ve mentioned before, if you have an MBA you’ve probably heard of him, but if you have a Ph.D. in Optimization, no dice. Engineers and scientists don’t go near this guy. Really, it’s too bad. They’re the ones teaching lean most of the time!
Let’s bring our hockey stick back for a second look to see what started to happen in the world Goldratt came on to the scene.

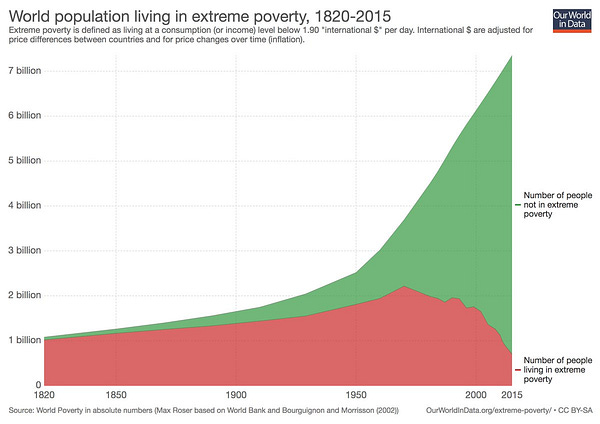
Keep in mind two things:
IMO one of the biggest contributors to things getting significantly better around 1950 seems to be the proliferation of the effects of production around the world (not during a world war, let’s say). Not everyone was operating lean, but people were starting to climb from artists to machine tools, and beyond.
All of our heroes, a.k.a. lean practitioners, a.k.a. product thought leaders, were born in exactly the right place at exactly the right time. Just as all of us are, right? Right. We’re getting there. One article and one step at a time.
Recall that Ford put together his lifelong thoughts on all things production in the book that reads like his legacy, Today and Tomorrow, which had 24 chapters. Taiichi Ohno read and re-read Ford’s work, built the Toyota Production System, and synthesized his thinking into just Seven Wastes and Ten Precepts. Later, Deming, in his uniquely profound way, put systems thinking ideas together in just four parts that he introduced to the world as the System of Profound Knowledge, which underlied his “New Economics.”
However, all of those principles last week seemed pretty abstract, didn’t they?
Despite how much Ford and Ohno built their systems from the bottom up, and despite how data-driven Deming actually was, no one had really come along to help out previously struggling manufacturing plants to turn the ship around - like completely around - start applying lean principles, and just start crushing it.
Goldratt created a formalized language and correspondingly lenses for lean thinking that he could put on any business. He called his language the Theory of Constraints (TOC for short), and it worked. It worked really freaking well. It worked so well, that after he used TOC to optimize manufacturing operations, he went further.
He abstracted.
He used it to optimize marketing and distribution.
Then he used it to optimize project management.
Then he used it to optimize enterprise resource planning and, yup, you guessed it, operations software.
And, knowing what we know about what the heck is up with Etsy, the lean startup, and the word product these days, it didn’t just work really freaking well. He epically crushed it, more than he could ever even know, since he died 11 years ago before FAANG was really a thing (MAANG? I digress).
Ok so he literally walked the path from the shop floor to walkways high above, to the other building where sales, marketing, and project managers sit, and he used the same systems and tools for each problem, just different input and output data.
But the physical principles at the root of optimizing systems of any kind remained the same.
Profound, huh?
Well, would it surprise you to know that he learned pretty much all of this when he was studying physics?
He was just the one guy that didn’t go around thinking that he was smarter than the business guys, that he might have something to learn.
As we’ll come to appreciate in time, the ability to make analogies across domains is one of the most unautomatable skills that we can learn in the 21st century. Machines can’t do it.
So how did he solve problems in different domains with the same systems and models?
Well, naturally, the data was different.
Goldratt was a 1980s data scientist 😝👨💻.
Welcome to Industry 3.5
I’m coining this Industry 3.5 term here to denote the union of two heretofore seemingly separate and distinct pieces of our production puzzle.
When we start going digital, things get crazy.
When Goldratt was in his peak, let’s say productive years, from the 1990s into the 2000s, is really when this connection started to become apparent. This is when commercial software was all of a sudden, on the rise.
The Theory of Constraints, fundamentally is based on continuous improvement. This is the essence of what still drives the data-centric, information-driven world in which we live.
Optimization 101. If you want to do better then you have to figure out what’s stopping you. A “constraint” is simply anything that limits the system from achieving its aim. As Deming would say getting all meta and profound, “without an aim there is no system.”
Goldratt was way out ahead of the game on this.
Around this time, the ideas of continuous improvement, lean thinking, six sigma, Total Quality Management (TQM), and Just In Time (JIT) started to come together. People started to realize that the same thing was at the center of all of this.
But Goldratt took it a step further, he realized like Elon does that a business is much more than operations and technology. Although he didn’t quite get to the whole “business as cybernetic collective” thing, he definitely unified the operations and sales & marketing sides of the house like no one before him.
Addendum 1 - The Actual Theory of Constraints
In the spirit of trying to holistically do a brief history, here’s the TOC system. There are only five focusing steps.
Identify the constraint
Exploit the constraint
Subordinate everything to the constraint
Elevate the constraint
Prevent inertia from becoming the constraint
It’s so simple, right!
Addendum 2 - Lessons Learned from The Goal
1. Operations are not The Goal for an entrepreneur, though they probably are for your process engineer.
Optimal flow is achieved through the plant when you produce exactly the right amount of your product, per unit time, in the right quantities, which are those that satisfy the majority of demand in the market but simultaneously hedge against losing money via inventory stacks that will immediately accrue as soon as there is an economic downturn.
2. When you do set out to optimize your throughput as you set up a business, you first need to develop a baseline.
That is, set everything up and see how much product or service that you can churn out per unit time.
Do not assume that you will be running at maximum capacity from day 1.
This almost never happens, and if you have orders for "at capacity," you will begin to run late on delivery almost immediately.
3. Aim at achieving harmonic flow states between machines in your manufacturing and other production processes, between your sales and operations teams, between the value delivered to your business and the value delivered to the market per unit of good sold, and also between your business and your community.
You might say that The Goal is to optimize what flows in, out, and through your business and the world that surrounds it.
From Leaning Out to Starting Lean
We’re not done with our journey, because just a few years before Goldratt passed away, another great thinker sprung onto the scene. The author of the Lean Startup, Eric Ries, apparently Steve Blank’s best student, became renowned the world over for his entrepreneurship, continuous innovation, and software startup practices that have since taken the world by storm.
In fact, in his most recent book, The Startup Way, he helped large companies practice intrapreneurship towards continuous transformation at companies as large as GE and the federal government. And in that book, he mentions that when he was visiting Toyota a few years back, he was told “This is the missing half of the Toyota Production System.”
You don’t say…
Share this post